Quality is defined from the customer’s perspective, and a proactive quality culture leverages QMS tools aimed directly at increasing customer satisfaction, such as, complaint management processes, risk management, compliance tracking.
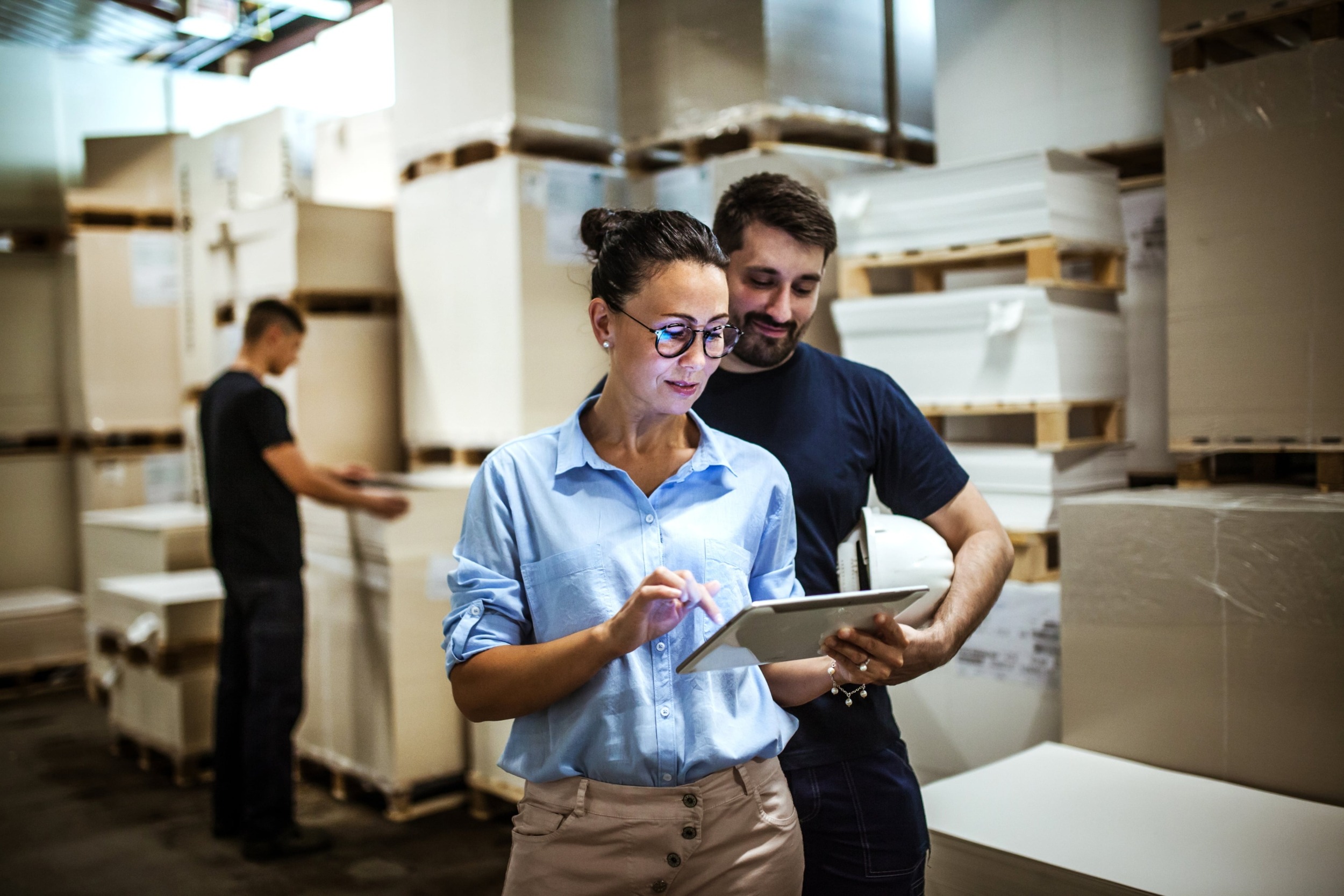
Get to Know ETQ Reliance QMS
What is a QMS?
A QMS is a collection of business processes designed to manage risk and productivity with consistent, repeatable outcomes.
What does QMS mean?
A quality management system, or QMS, is a formalized system of processes and procedures designed to improve quality throughout an organization — with the end goal of better meeting customer requirements and improving customer satisfaction.
In particular, effective quality management systems help businesses to implement practices like Total Quality Management (TQM) and comply with regulatory standards like ISO 9001.
QMS vs. QMS software
Don’t confuse the QMS with QMS software.
A QMS is a set of processes and procedures — and many QMS are still based in pen and paper or ad-hoc spreadsheets. But organizations are increasingly digitizing quality management software, also known as eQMS Software.Â
Typical quality management software platforms are workflow-based and provide intelligent routing to move quality-related events through different areas of the business to ensure product or service quality.
Most QMS systems consist of a variety of applications, including:
- Document control
- Audit management
- Nonconformance tracking
- Corrective action
- Employee trainingÂ
However, more comprehensive QMS solutions encompass critical processes like supplier quality, quality events, and new product introduction (NPI).
Each designed to accomplish a specific task. For example:
- A document management application stores and organizes controlled documents.
- A corrective action (CAPA) application helps quality managers direct correction of nonconformances of all types.Â
- A training management software stores and distributes training data while tracking workers’ progress against the required courses to operate equipment and safely navigate the industrial environment.
A QMS also enables quality automation, which minimizes human error across repeatable processes and ensures quality throughout product and business life cycles for companies of any size. Quality automation is a dynamic process that deploys highly integrated technology solutions to improve organizational efficiency, reduce costs, deliver higher quality products, and better services across your organization’s business divisions.
Achieve Total Quality Management with a QMS
Total Quality Management is a management approach businesses can adopt to achieve long-term success through customer satisfaction. Under this approach, all members of an organization participate in improving processes, products, services, and the culture in which they work.
The American Society for Quality (ASQ) defines eight principles of total quality management. Companies that adopt these principals — and other process excellence methodologies — rely on a variety of QMS tools to deliver.
1. Customer focus
2. Empowered employees
An engaged workforce is the engine that drives TQM. The QMS helps all employees take ownership of quality by providing data and feedback on how their efforts impact quality.Â
3. Process approach
Like many quality philosophies, TQM draws from the process approach aimed at understanding the link between process inputs and finished quality. A QMS supports the process approach by addressing every element of the Plan-Do-Check-Act cycle.
4. Integrated Systems
TQM emphasizes the connection of different functions and process areas into an integrated business system. A fully integrated QMS ties together the full range of quality processes, also moving data to and from other business systems (like ERP and MES).
5. Strategic management
Companies must have a strategic plan that makes quality a top priority. That means including quality and risk data in management reviews, including quality initiatives in the budget, and communicating results regularly.
6. Continuous improvement
The QMS supports continuous improvement, but only if you have a closed-loop process to address issues you find. An automated QMS holds a distinct advantage over manual tracking and follow-up methods.
7. Data-driven decision-making
TQM focuses on making decisions based on performance data. A proactive organization will collect and analyze data on an ongoing basis, using integrated Reporting tools to analyze trends and take action.
8. Communication
The final element of TQM is communication. QMS automation can help here, ​​so that all employees know about updates, policy changes, and new processes. This prevents information silos, and it helps more accurately measure the effectiveness of current policies and procedures. The communication process must include all front-line employees, to whom performance data matters just as much as it does to leadership.
The final element of TQM is communication. QMS automation can help ensure that all employees know about updates, policy changes, and new processes. The communication process must include all front-line employees, to whom performance data matters just as much as it does to leadership.
An advanced QMS system helps companies to realize a variety of benefits, such as the following.
Streamlining the transition from quality as a cost center to quality as a driver of enhanced financial performance.
Connecting elements of quality across departments and breaking down data silos to improve production inefficiency.
Providing structure for a worker-focused approach to training, safety, and operations.
Leveraging customer complaints to inform product improvements and messaging.
Serving as catalyst to organization-wide digital transformation through enterprise integration and advanced, actionable analytics.
Helping the business to develop healthy, productive, and honest relationships with suppliers and customers.
How to select a QMS: 7 factors to consider
As demand for QMS grows, so does the vendor landscape, complicating decisions over the right choice that ensures a successful implementation and facilitates mission-critical quality initiatives.Â
In fact, research shows 71% of software rollouts fail, are late or are over budget.
To make sure you find the right QMS, make sure you clearly define your needs up front, and consider the following factors in your prospective vendors.
- Flexibility. Operational excellence demands a QMS flexible enough to change as your processes continue to evolve in the future.Â
- Web-Based vs. web-enabled. Web-based software allows users to access all forms, workflows and applications — including administration — through a web browser. This allows anywhere access. Web-enabled software may use third-party tools or middleware to mimic a web-based experience, but still requires installation on every computer.
- Secure collaboration with external partners. It’s vital to be able to streamline your supplier quality process with controlled access to your QMS.
- Accessible reports and analytics. For many vendors, reporting is an afterthought that involves third-party tools with limited QMS integration. A more robust QMS will have reporting tools embedded in the software, allowing you to pull data across the system for actionable insights.
- Integration. From production to financial to quality systems, collaborating and sharing information enterprise-wide is key to uncovering process gaps and maximizing the business value of a QMS.
- Scalability. Even if it’s not an immediate need, the ability to expand your QMS to other facilities, suppliers and customers makes a huge difference in overall value.Â
- End user experience. Make sure your selection process takes into account the user’s experience, including customizing your QMS with your organization’s visual guidelines.The user experience should be intuitive and holistic, and enhance productivity.