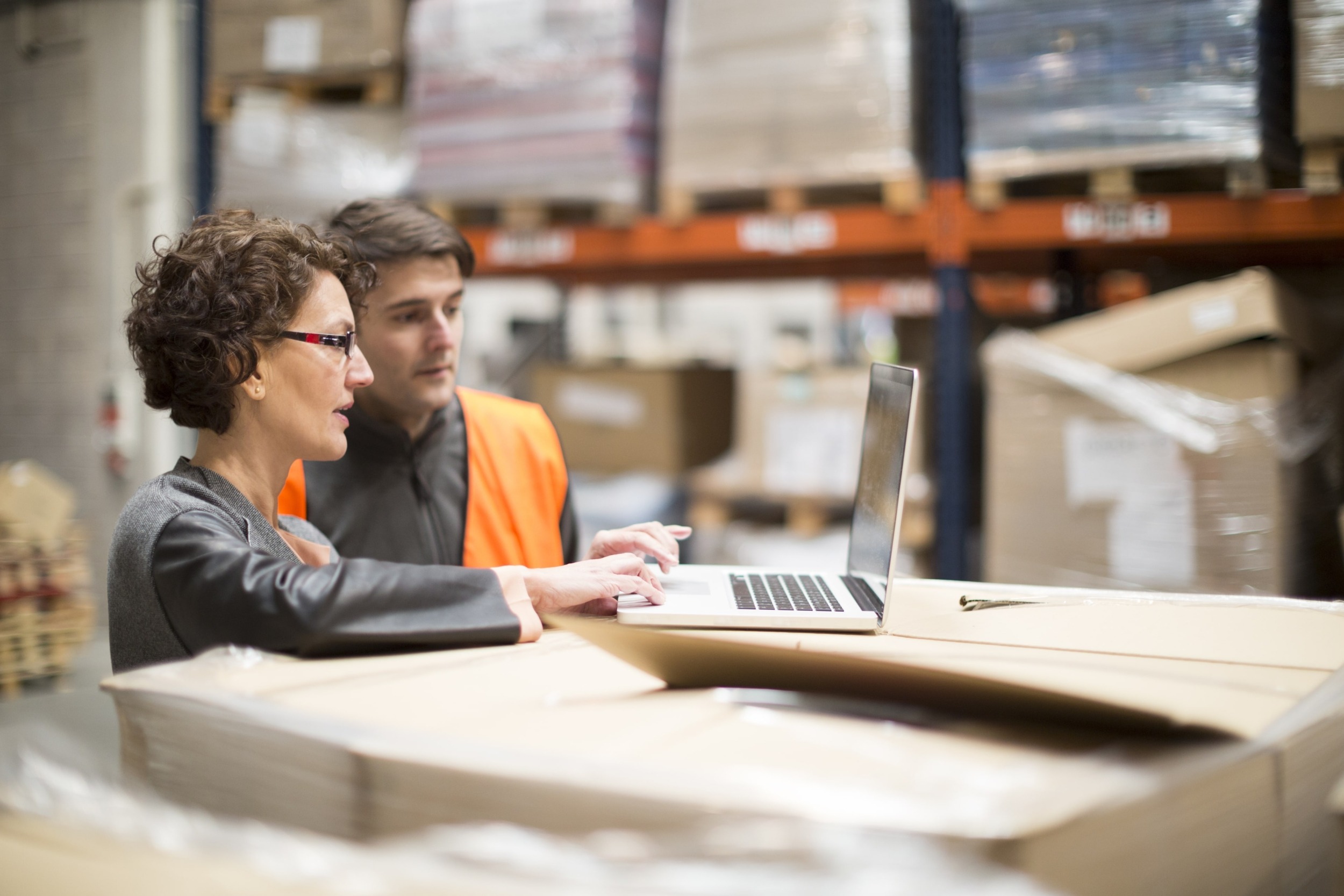
Manufacturers across almost every industry experience a vast demand for products, meaning facilities, workers, and machines are being pushed to maximize output. That increases the likelihood of process failures and the consequences when they occur. Despite the push for speed, however, organizations cannot hurry the root cause analysis process.
When failures occur, it might not be because a worker forgot to read the safety manual or because a belt was stressed beyond its operating limit. Instead, the root of the problem might be systemic—the manual might have been on an inaccessible computer, the belt may have been improperly sourced from the supplier. Root cause analysis means going past the apparent source of the problem, uncovering deeper issues to increase quality and safety at the organizational level.
Getting Started with RCA
Five Steps to Performing Root Cause Analysis
Root cause analysis is multidisciplinary because apparent problems with a product or process can originate in almost any part of the organization. That can initially be daunting—there’s much ground to cover during the product lifecycle—but a relatively simple five-step process can narrow it down.
Although the process below is straightforward enough, it usually requires knowledge from different parts of the organization. The best practice is to create a cross-functional team. The team’s composition may be different with every incident because it should always include individuals who work with processes connected with a product failure or quality event.
- 1. Start by defining the problem
What happened? The RCA team should begin by documenting and contextualizing the incident—not just what happened, but any warning signs that the event might happen beforehand. - 2. Measure the impact
Is this a single incident or part of a pattern of similar failures? Understand the extent to which the specific incident (or incidents) affects the organization—whether by causing unplanned downtime, diminishing customer trust, incurring compliance violations, affecting worker safety, or all of the above. - 3. Determine contributing factors
A single problem can have multiple causes. A defective product may have been caused by inadequate worker training and a failure in the automation system. - 4. Understand the root cause
Take the data you’ve collected above and place it into a fishbone chart, a “5 whys” process, or a Pareto chart—the three primary root cause analysis tools. Use their output to help you determine the primary causes of an incident. - 5. Create a solution
Depending on the results of the analyses above, create a solution that mitigates or eliminates the original problem.
Looking for an easy-to-use Root Cause Analysis Toolkit? We’ve created one for you here.
Add RCA to Your QMS
Use ETQ Reliance NXG to Create a Formalized Root Cause Analysis Process
Regardless of what occurred or whom it affected, quality managers should deploy a consistent and repeatable process for root cause analysis. The Corrective Action application within ETQ Reliance makes it faster and easier to get accurate results from RCA.
Organizations should not rush root cause analysis—but there’s also no denying that the present-day manufacturing environment demands more speed. By integrating your RCA process into a cloud QMS in the form of Reliance NXG, quality leaders can have it both ways. They can have detailed and accurate analyses from the traditional RCA process and the speed and analytical focus demanded by industry 4.0.
In other words—Reliance NXG provides a centralized hub for all quality data, destroying data silos in the process. As such, it’s much easier to identify the problem, identify the impact, and find contributing factors. All this data is at the tips of your fingers with a modern QMS that can automatically tag data related to a nonconformance or process failure and deliver it to you. From there, you can use ETQ’s built-in analytics tools to understand your issue and find a fix.
Not sure how to get started with Root Cause Analysis? Consult with an expert and we’ll get you on your way.
Three Tools for Root Cause Analysis
Built-In Analytics from ETQ Makes RCA Easy
Quality doesn’t start on the factory floor—it starts during product design. ETQ’s RCA tools allow organizations to trace product failures throughout the entire product lifecycle, allowing them to inject quality into every part of the process.
ETQ Reliance offers three primary tools for root cause analysis—fishbone diagrams, Pareto charts, and 5 whys. These tools are fundamental to RCA and have been in quality management toolkits for decades. However, the increased complexity of the manufacturing process threatens to overwhelm their utility.
With ETQ, users can rapidly assemble the data necessary to populate these fundamental RCA tools and understand where process failures and nonconformances originate. From there it’s a vastly more efficient step to creating more streamlined processes and accelerating the continuous improvement process to get ahead of emerging issues.
Learn more about ETQ Insights, our advanced quality analytics solution.
One of the key requirements when we bought ETQ was that we could use it for supplier management. Our supplier quality engineering group is extremely happy with ETQ. We are going after a market that requires zero defects (automotive market). It’s a different standard—and ETQ hits that standard.
Root Cause Analysis FAQs
What is the definition of root cause analysis?
Root cause analysis (RCA) is analyzing a problem until the originating factor is isolated. For example, a manufacturer might experience problems like nonconformance, a manufacturing defect, an accident at a job site, or a failure to reach production goals. Dozens of separate factors might cause these problems, but these factors cascade from one or two sources at most. Eliminating these sources fix the downstream problem at your organization—if you conduct the root cause analysis correctly.
How can I conduct a root cause analysis?
Finding the source of the problem requires several careful steps. First, you must identify the problem you want to investigate, which includes defining the impact and duration of the problem. Next, assemble a team of investigators. These should consist of people familiar with RCA, who know about the process under investigation, and who aren’t involved in the incident itself—this will help ensure a fair and nonbiased review process.
Investigators will use one of five root cause analysis tools to identify and eliminate the source of the problem. Ideally, the review team reconvenes periodically to ensure that their analysis accurately identified the source of the problem and that it did not recur.
What are the five root cause analysis tools?
- Five Whys Analysis
This process invites the review team to ask why an incident occurred until no other possible causes are left. This analysis is an easy way to narrow down the cause of an incident to a single factor. - Pareto Chart
This bar chart arranges the cause of various incidents according to frequency, time, or cost. The idea is that most incidents depend on a small number of root causes—eliminate those, and you’re left with a much more efficient process. - Fishbone Diagram
Use fishbone diagrams in complex problems where there may be many root causes. Here, the problem is written at the end of an arrow, and major contributing factors are written as branches. This diagram allows you to create a comprehensive plan addressing every aspect of an important issue. - Scatter Diagram
This simple diagram plots out a relationship between cause and effect to see if there’s a correlation. For example, you might create a graph that correlates the relationship between nonconforming material incidents and hours of unplanned downtime. If the points make a line, then you may have landed on a significant variable.Failure Mode and - Effects Analysis (FMEA)
Although this is not a root cause analysis tool per se, FMEA allows quality managers to understand the possible effects when a product or process fails. The title explains most of it—this is the process of understanding how something fails and what happens when it does. The advantage of this is, if a failure occurs in real life, it is that much easier to trace the effects of that failure back to a corresponding root cause.
When is the best time to conduct a formal root cause analysis?
The best time to conduct a root cause analysis is as soon as possible—but with that said, different RCA team members have different schedules. You shouldn’t sacrifice the experience or impartiality of your RCA team by picking team members based on immediate availability. You should wait for the most ideal candidates to become available instead of picking team members based on who has free time.
Memories fade quickly, making it seem like there’s some urgency when starting an RCA process. One way to counteract this is to record or transcribe interviews with involved personnel within days or hours of a serious incident. This strategy allows the RCA team to review these recordings at their leisure once the formal process begins.
How do you write a root cause analysis?
A root cause analysis is a complex process involving many stakeholders. The simplest way to track this process is to use a checklist. If you’re using a quality management system (QMS) with your RCA process, a checklist for RCA will likely be included with its CAPA application. Otherwise, many organizations have RCA checklists and templates available for free.
What are the Five Whys of root cause analysis?
The “Five Whys” is one of the most popular methods of root cause analysis. It seeks to boil down a quality incident to a single root cause. This strategy involves first asking why the incident happened—a sample answer may be that a piece of equipment wasn’t maintained. Then this method asks why the equipment wasn’t maintained—maybe no one was explicitly assigned to maintain it—and then it asks why no one was assigned. The point is to keep asking “why” until you ask, and when you can no longer ask “why you’ve reached the root cause of your problem.
What is the best root cause analysis method?
The best root cause analysis method is the one that fits the incident you’re reviewing. Some incidents are systemic—think of incidents like a production slowdown or a failure to reach quality benchmarks. These incidents are likely to have more than one root cause. An RCA method, like a Pareto chart, might give you more insights. Meanwhile, an incident that may have just one root cause—such as an accident causing an injury—might be more suited to evaluation using a Five Whys analysis.