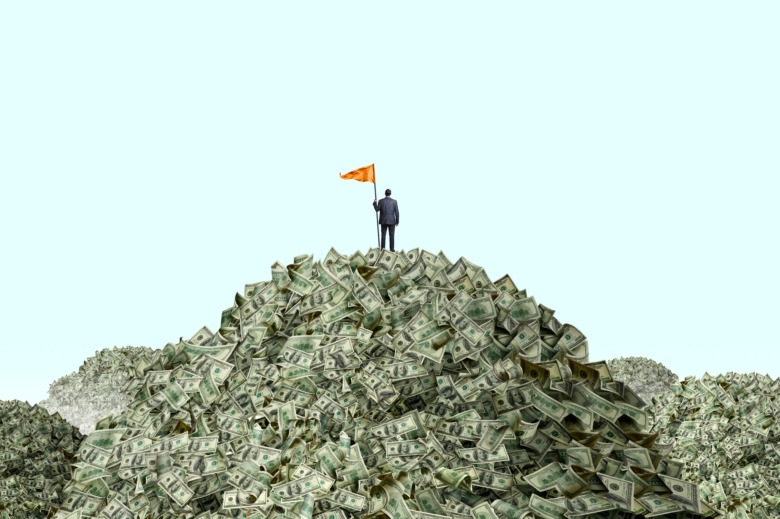
Webinars – 60 min
Cost of Quality and Your Bottom Line
Learn the journey of Owen Mumford and Corning, Inc when they were choosing and implementing a quality management system. You’ll also learn the savings and benefits they realized from a flexible and scalable quality management system.