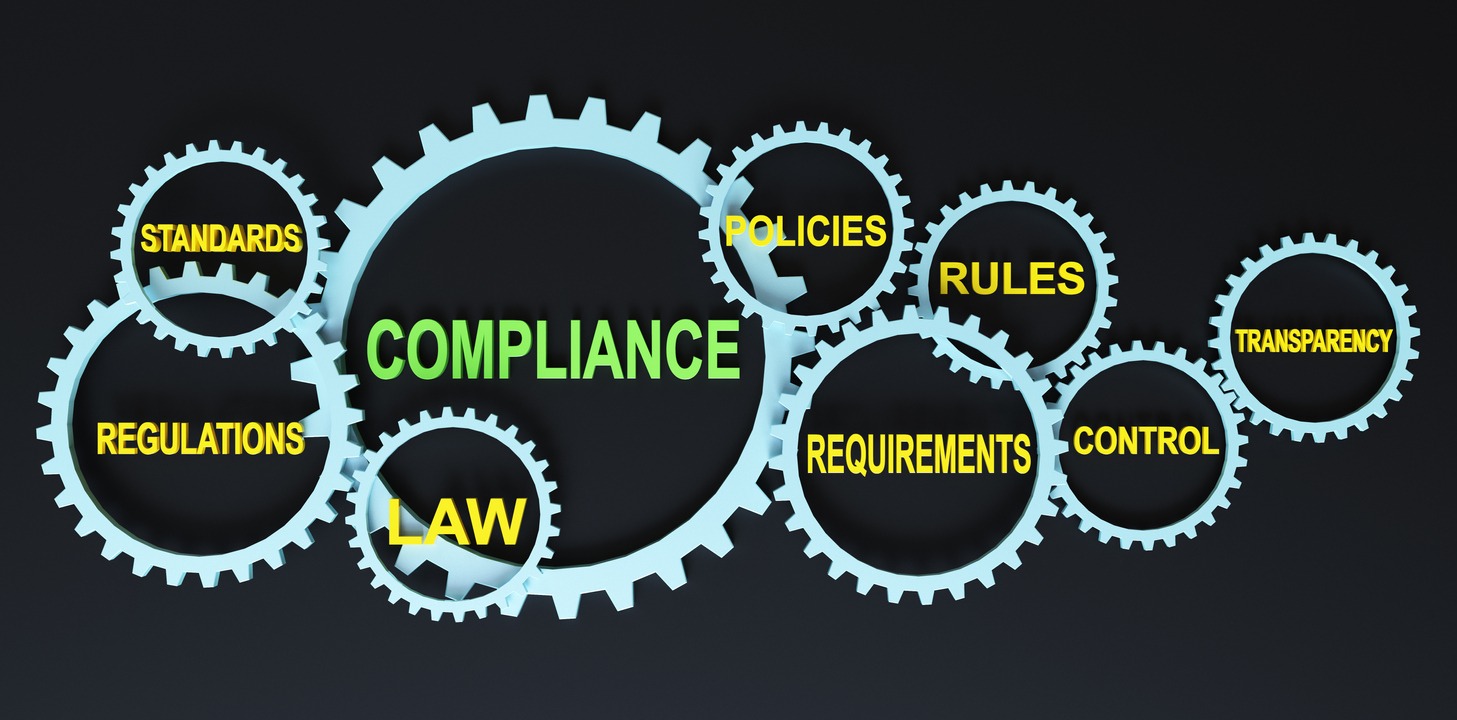
A
Acceptance number: The allowable number of defects in a sampling lot. Exceeding this number means the lot is not acceptable.
Acceptance quality limit (AQL): The acceptance number averaged over a series of lots. Exceeding this limit means the process is no longer satisfactory.
Acceptance sampling plan: Plan defining the number of items sampled in a lot and what constitutes an acceptable or unacceptable item. That may also include the order of lots and the number of lots in a sample.
Accreditation: The process of certification, in which a reputable entity determines that an organization can deliver specific services safely and competently. The specific definition of this process changes on a per-industry basis.
Activity-based costing: The total cost of designing, ordering, and manufacturing a product.
Activity network diagram: a planning process using an arrow diagram.
Advanced Product Quality Planning (APQP): A process used to guarantee quality through the design and sourcing process for automotive manufacturing.
Adverse event: A term the healthcare industry uses referring to any undesirable and out-of-the-ordinary incident in the context of operations.
Aerospace quality: Any quality guideline, such as the SAE Aerospace Standards, signed specifically to enforce quality in aerospace manufacturing and operations.
Aerospace Quality Management Systems (QMS): Any quality management system designed to impose and improve aerospace manufacturing best practices.
Agile: A project management methodology—usually specific to software development—focusing on speed and continuous improvement.
American Customer Satisfaction Index (ACSI): An economic indicator that has measured consumer satisfaction in the United States, across industries, since 1994.
American National Standards Institute (ANSI): The entity representing the United States within the International Organization for Standardization (ISO). Administrates voluntary standardization within the country.
American National Standards Institute-American Society for Quality (ANSI-ASQ): The organization responsible for accrediting the bodies responsible for certifying quality and environmental management systems under ISO 9001 and ISO 14001.
American Society for Testing and Materials (ASTM): A nonprofit offering a discussion group that creates voluntary standards for products, systems, services, and more.
American Society for Training and Development (ASTD): A U.S. organization dedicated to providing classroom materials and training for workers learning on the job.
Analysis of means (ANOM): An advanced control chart designed to help citizen data scientists understand variance when troubleshooting workflows and creating new processes.
Analysis of variance (ANOVA): An analytics tool (the precursor to ANOM) designed to point out how a factor or factors contribute to overall variation.
ANSI ACS X12: A standard used to govern how organizations communicate with customers and deliver shipping notifications.
Appraisal cost: Essentially, measuring quality is the cost of determining whether the quality organizations deliver matches the level of quality customers expect.
Arrow diagram: A kind of flow chart used to map out workflows. It’s often used to organize planned activities in sequence and chart a critical path through nodes.
Assessment: The process of ensuring that an organization or product conforms to a quality benchmark.
Assignable cause: An identifiable source of deviation—unrelated to random probability—within a process.
Attribute data: An aggregate of conformance data that determines whether to halt or continue an industrial process.
Attributes, method of: A quality control method uses a unit’s measurable attributes—e.g., its internal diameter—and uses this metric to determine whether the unit passes inspection.
Audit: An inspection intended to verify whether an organization, its products, or its services comply with standards set down by a third-party governing body.
Audit software: Any software, such as document control, that’s designed to help quality managers respond to audit requests.
Automotive Quality Management System (QMS): Any quality management system designed to enforce and improve best practices related to automotive production. See also: PPAP.
Autonomation: An automated quality process in which machines inspect products and components. These machines receive the authority to shut down production and alert supervisors when they detect a nonconformance.
Average chart: A control chart variant where process stability is evaluated using the subgroup average.
Average outgoing quality (AOQ): A quality metric that compares the quality of a finished product with the quality of its constituent components.
Average outgoing quality limit (AOQL): This is the maximum level of quality that a finished product can achieve based on average incoming quality.
Average run lengths (ARL): A control chart metric that denotes the number of inspections that must take place before a shift in magnitude occurs.
Average sample number (ASN): The approximate number of sample units requiring inspection per lot before reaching a go/no-go decision.
Average total inspection (ATI): The average of all units inspected in all lots, including lots that have been discarded for nonconformance.
B
Balanced plant: A facility containing exactly enough raw materials to create the exact number of products that the market demands.
Balanced scorecard: A system for continuous strategic improvement based on top-down management regarding internal workflows.
Balancing the line: The process of balancing available work across available resources, preventing them from stagnation or overuse.
Basic quality concepts: The basic tools for determining product quality, including failure mode and effects analysis, corrective action management, risk assessment, and more.
Batch and queue: The process of intentionally overproducing components and then staging them at the next operational area before being immediately used.
Benchmarking: The process by which an organization determines the level of quality achieved at market-leading organizations and then replicates their processes.
Benefit-cost analysis: A study designed to determine whether improving a product costs more than any increase in revenue because of improved customer satisfaction or functionality.
Best practice: An agreed-upon cross-industry method that supports process improvement within an organization.
Block diagram: A graphic that displays the operational components of a workflow. Each block is a component, and each connecting line is an interface.
Board of Standards Review (BSR): The board is responsible for creating new American National Standards and revoking old ones.
Box and whisker plot: A data visualization used to identify statistical outliers by highlighting information between the 25th and 75th percentiles
Breakthrough improvement: More than a gradual improvement—a sudden and intentional performance increase to a greater quality tier.
Business process reengineering (BPR): The act of reworking business processes to meet new or existing KPIs.
C
Calibration: The process of tuning a measurement tool by comparing its output to a tool with known accuracy.
CAPA program: A program (software or otherwise) designed to implement and document corrective action taken in the wake of an accident or nonconformance.
Capability: This metric represents the amount by which a process can vary while remaining stable. Often used in conjunction with control charts.
Capability maturity model (CMM): A plan that governs the development of software processes from immaturity to maturity and effectiveness.
Capacity constraint resources: Any constraint on the output of the process, other than a bottleneck.
Cause: The identifiable origin of a process error or nonconformance.
Cause and effect diagram: Also known as a “fishbone diagram,” this visualization points out the causative factors leading to a process error or defect. It’s one of the main tools in corrective action.
Cell: A (typically U-shaped) arrangement of workers and capital equipment. Components and raw materials are flowed through this arrangement and are processed.
Cellular manufacturing: A manufacturing process in which capital equipment and operators are placed within a U-shaped cell, and materials for processing are delivered from without.
CE marking: This mark, which stands for “Conformitè Europëenne,” designates a product that conforms with regulations allowing it to be sold within European Economic Area.
Central tendency: A statistical phenomenon in which the value of most data aggregates toward the median.
Chain sampling plan: Whereby the acceptance of a lot depends not just on its sample results but also on the results of the lots before it.
Change management: Changing a product design, process, or workflow within an organization while creating minimum disruption and preserving or improving quality.
Change management software: Any software intended to assist processes changing product designs, processes, or workflows within an organization.
Changeover time: How long it takes to tear down and set up a process component during a routine or unscheduled change.
Checklist: A list of items individuals must check off (in order) before a process-critical operation can get underway.
Check sheet: A basic data collection tool allowing workers to quickly understand the output of a process or a workflow and learn whether it’s in normal bounds.
Classification of defects: A series of categories defining how a unit may be defective, ranked from least to most seriousness.
Cloud QMS: A software-based quality-management system designed to be hosted in the public or private cloud.
Common causes: Any inherent qualities of a process that can cause the outcome to vary.
Complaint handling system: A system designed to collect and respond to complaints from customers or internal users.
Complaint tracking: The process of collecting internal or customer complaints, distributing complaint forms, and then collecting data on the resolution process.
Complaints management software: A software system designed to help the service desk collect and respond to customer complaints.
Compliance: The process of adhering to regulations, governance, standards, specifications, and more.
Concurrent engineering (CE): The process of speeding up the design of a new product by developing multiple systems simultaneously.
Conformance: A product or service that has passed inspection and met its legal, contractual, or regulatory obligations is in conformance.
Conformity assessment: The act of assessing whether a product or service can pass inspection and meet its legal, contractual, and regulatory obligations.
Constraint: A bottleneck that prevents a system from increasing its throughput or productivity.
Consumer’s risk: When a customer receives a product that doesn’t meet specifications or function as designed. This risk grows or shrinks as an organization changes its sampling and inspection procedures.
Continuous flow production: A manufacturing process where components are moved from one station to another in batches of one, and each station performs the operations needed by the next one.
Continuous improvement (CI): A quality management philosophy in which quality is not held static—instead, each aspect of quality must show improvement as time goes on.
Continuous improvement software: Software designed to assist in continuously strategizing and implementing improvements in a quality management program.
Continuous sampling plan: A sampling process in which every product is inspected as it’s produced. This process continues until a certain number of products pass inspection in a row.
Control chart: A graph of productivity, defects, or other values over time. As these values increase or decrease towards the upper or lower boundary of the chart, the processes that they record become more or less stable.
Control plan (CP): Instructions for maintaining the quality of both parts and processes within a manufacturing system.
Corporate governance: The normative processes of an organization serving to increase balance competing priorities such as quality, productivity, revenue, customer satisfaction, and more.
Corrective action: The act of mitigating a problem with a process, a supplier, a product design, and more.
Correlation (statistical): Not to be confused with causation. Two variables with an apparent relationship.
Cost of poor quality (COPQ): The cost—including fines, loss of revenue, and remediation—of shipping a product or delivering a service that doesn’t conform to customer expectations or function as designed.
Count chart: A control chart variant that evaluates process stability by counting quality events within a given sample.
Count per unit chart: A control chart variant evaluating process stability by averaging the number of quality events within a sample.
CPG: Also known as consumer packaged goods, these are products used and replaced regularly and sold to consumers rather than businesses. Food and beverage, paper towels, and some clothing items are all good examples of CPG.
CPG Quality Management: A quality management system designed specifically to promote and improve consumer packaged goods manufacturing quality.
Critical incident: An advanced root cause analysis technique that involves interviewing personnel involved in a critical event.
Critical processes: Any process which can potentially endanger life, poison the environment, or entail a significant loss of revenue and (or) reputation.
Current good manufacturing practices (CGMP): Regulations specific to F&B and (or) pharmaceutical industries. It is enforced by the United States Food and Drug Administration (FDA).
Customer relationship management (CRM): Not to be confused with CRM software, customer relationship management is designed to gather intelligence about customers, build more accurate personas, integrate information from multiple channels, and ultimately build closer customer relationships.
Cycle: any workflow designed to repeat—once an hour, once a day, once a week, or as needed.
Cycle time: The timeframe to complete a single cycle.
D
Data collection and analysis: The process of selecting data and methods for analytics.
Data collection and analysis tools: The physical charts and related software designed to collect data and display it in an interpretable context.
Decision matrix: A data visualization designed to help teams choose a method for solving problems or optimizing processes. Teams list methods on one axis and criteria on the other and then score each criterion from one to five. The methods with the highest scores deserve the most consideration.
Defect: An aspect of a product or component which does not look or function as expected. Defects are ranked by class and range from cosmetic (class four) to catastrophic (class one).
Dependability: A product or machine is dependable to the extent that it can be used to the full extent of its designed functionality at any random time.
Deviation: The gap between a data point and the central tendency of a data set.
Diagnosis: The process of determining the root cause of a deficiency via data collection, analytics, and experimentation.
Document Control: The process of creating, revising, approving, and retracting critical documents such as training materials or operating instructions related to the manufacturing environment.
Document Control Software: Any software system that assists the process of creating, revising, approving, and retracting critical documents such as training materials or operating instructions related to the manufacturing environment.
E
Eighty-twenty (80-20): Also known as the “Pareto principle.” This observation indicates that in many cases, most effects (80%) descend from a minority of causes (20%).
Employee training management software: Any software that helps disseminate training materials, keeps them up to date, and tracks employees’ progress as they complete training documents.
Environmental health and safety (EHS) software: Any software that helps companies measure their impact on the environment, set goals to mitigate environmental impact, and track their progress towards meeting those goals.
Environmental management system: The set of intentional actions that an organization takes to mitigate its environmental impact.
Equipment availability: Also known as uptime, this metric measures how often a piece of equipment can run. That’s calculated in percentages—”five nines uptime” means that equipment is available to run 99.999% of the time.
eQMS: Any software-based quality management system.
Error detection: A system in which defective products or components are identified as soon as they’re assembled. Once identified, the assembly process halts and won’t resume until the source of the error is mitigated.
Error proofing: The process of creating an improved product design that prevents errors from being made in the first place.
Experimental design: A quality process that involves changing variables such as tools and conditions to find a better outcome.
External failure: Any defect or nonconformance that originates outside of the manufacturer. For example, a defect occurring because of a nonconforming shipment from a supplier.
F
Failure cost: The costs that incur when a product or component is defective—which may include costs of a recall, cost of auditing a supplier, reputational costs, and more.
Failure mode effects analysis (FMEA): The process of mapping out potential product failures and their ramifications. That also includes the process of understanding how to mitigate failure risks.
Feeder lines: Tributary assembly lines that feed into the main assembly area. These lines let workers and machines perform prerequisite tasks that must be completed before assembly while reducing the number of components on the mainline.
First in, first-out (FIFO): Inventory management system which queues the oldest materials in storage for subsequent use. This system is standard with perishable items which must be used before they expire.
First pass yield (FPY): The ratio of products that pass inspection to total products produced.
First-time quality (FTQ): See “First pass yield.”
Flowchart: A process diagram showing steps in boxes, which connect by arrows to illustrate how they proceed.
Focus group: An organization of up to ten people representing the customer base. They’re asked to give their opinion about an existing or upcoming product. Their feedback provides input during the design phase.
Food safety management: Managing the food and beverage manufacturing process to comply with FDA guidelines and ensure customer health and safety.
Food safety software: Any software program, such as a QMS, explicitly designed to enforce quality and safety within food and beverage production.
Frequency distribution (statistical): A graph designed to highlight the average of a data volume and its distribution.
Functional layout: Distinct from cellular manufacturing, this manufacturing practice groups machines by the function that they perform.
Functional verification: Ignoring cosmetic blemishes, this kind of inspection ensures that a part performs as designed.
G
Gantt chart: A bar chart used as a project management tool to display overall progress on a planned task.
Gap analysis: A report analyzing the difference between the business at present and its desired future objective.
Geometric dimensioning and tolerancing (GD&T): A collection of rules that apply to engineering drawings and illustrate how parts relate to one another.
Good laboratory practices (GLP): A set of regulatory practices for laboratories intended to ensure that tests are performed safely and consistently, ensuring repeatable results.
Good manufacturing practices (GMP): A set of regulatory practices intended to ensure that manufacturers reliably produce safe products that meet customer requirements.
H
Hazard analysis and critical control point (HACCP): U.S. food safety management system designed to promote quality and traceability within the F&B manufacturing industry and enforced by the FDA.
Highly accelerated life test (HALT): A destructive testing process that used high vibration and extremes of temperature to understand how a product is likely to break during regular use.
Highly accelerated stress audits (HASA): A technique where some (but not all) product subassemblies are subjected to HALT-style testing to determine how changes to these subassemblies impact the overall quality and functionality of the finished unit.
Highly accelerated stress screening (HASS): A process similar to HALT but involving nondestructive testing.
Histogram: A bar chart representing the way that numerical data is distributed throughout a range.
I
IATF 16949: A supplier quality management system for OEMs in the automotive industry. Replaced ISO/TS 16949 in 2016.
Impact effort matrix: A problem technique creating a four-quadrant X/Y chart denoting the possible solutions to mitigate a known problem. It allows quality managers to find the solutions with the highest impact and the least effort involved in implementation.
Inspection: The act of verifying that a product or service complies with its designed specifications.
Inspection cost: The cost of verifying that a product or service complies with its designed specifications.
Inspection lot: A group of products, components, or raw materials examined to verify whether they conform to their required specifications.
Internal failure: Any product failure occurring during production, assembly, or staging, before a user outside the organization, receives the product.
International Aerospace Quality Group (IAQG): A trans-national group dedicated to promoting continuous quality improvement within the aerospace industry supply chain to increase quality and reduce cost.
International Automotive Task Force (IATF): An association of automobile manufacturers and related organizations created to promote quality throughout the industry.
International Organization for Standardization (ISO): A unifying international standards body formed to promote voluntary quality guidelines for manufacturers across industries.
ISO 14000: A family of voluntary regulations created by the ISO group and designed to promote environmental health and safety.
ISO 19011: A voluntary guideline created by the ISO group and designed to create a standard for auditing management systems.
ISO 26000: A voluntary guideline created by the ISO group and designed to promote social responsibility.
ISO 9000 series standards: A family of industry-agnostic guidelines created by the ISO group and designed to promote creating effective quality management systems. Several revisions have occurred, including ISO 9000:2005, ISO 9004:2009, and ISO 9001:2015.
J
Job instruction: Quality process information that specifies the duties performed in a specific job function.
The Joint Commission: An organization authorized to accredit healthcare organizations in the United States.
Just-in-time (JIT) manufacturing: A manufacturing process that emphasizes meeting customer demand while holding as little inventory on hand as possible.
Just-in-time (JIT) training: The process of training a worker or user immediately before they perform a task, ensuring it’s nearly impossible for them to forget what they were trained on.
K
Kanban: An inventory control process that supports lean or just-in-time manufacturing by limiting the amount of work in process inventory.
Key performance indicator (KPI): A metric that indicates whether an organization upholds organizational goals such as productivity, quality, or customer satisfaction.
Key process: A process of significant importance, one making a substantial contribution to upholding organizational goals.
Kitting: The process by which assembly line workers are pre-supplied with the tools and components needed to perform a task, eliminating the time spent searching for materials.
L
Laboratory scope: A document listing the extent to which a laboratory can control its quality by using tests, equipment, and voluntary or mandatory standards.
Last off part comparison: A method to standardize quality levels by comparing the last part from a production run with a random part from the subsequent run.
Layout inspection: A record containing the totality of all measurements in a design.
Lead time: The time between customer order placement and delivery.
Lean: A system designed to use the smallest amount of excess material in manufacturing while preserving (or improving) production speeds.
Lean manufacturing/production: A system designed not just to eliminate wasted material in manufacturing but also to eliminate wasted time, minimize inventory on hand, streamline batch sizes, and more. To accomplish this, companies focus on continuous improvements in quality.
Lean migration: The process of implementing a lean production system.
Level loading: A concept from lean manufacturing. Companies streamline their production, producing the same number of units every day—meeting customer demand without varying production volumes.
Load-load: A system in which a single operator can complete several steps in production by moving parts between machines in sequence.
Lost customer analysis: The process of investigating factors related to customer churn.
Lot: A consistent number of units going through the production process and then be sampled for quality testing purposes.
Lot quality: The number of defective units per one hundred units within a lot, as expressed in a percentage.
Lot tolerance percentage defective (LTPD): The lowest acceptable lot quality for a lot that ships to the customer.
M
Maintainability: The extent to which a machine can be serviced or repaired. For servicing, maintainability means that a machine can be inspected and maintained within the scope of planned downtime. For repairs, maintainability means that a machine can be repaired while minimizing unplanned downtime.
Manufacturing quality: The concept of imposing best practices on a production system to ensure the end result meets or surpasses customer and regulatory requirements.
Manufacturing quality management system: Any QMS designed explicitly for manufacturers (as opposed to service providers) and intended to impose best practices on the production system.
Manufacturing resource planning (MRP II): The process of harnessing finance, capacity planning, and requirements planning to create a tool that simulates alternative production plans.
Material handling: Any method of moving materials from one machine to another or assembly to staging within the manufacturing environment.
Material requirements planning (MRP): A digital manufacturing assistant that helps deliver the correct number of units to the right stage of the production process at the right time.
Mean time between failures (MTBF): The average amount of time between one failure (in production equipment) and the next.
Medical device quality management system: A QMS designed to impose best practices on a medical device manufacturing process such that the resulting product improves patient health and safety per local regulatory guidelines.
Mistake proofing: The process of improving machines, training, or manufacturing processes to prevent defects or operator error. That’s distinct from error proofing, which is the process of preventing defects by addressing the product’s design.
N
National Institute of Standards and Technology (NIST): A U.S. Department of Commerce agency with authority to create standard measurements and operating standards that govern everything from building codes to cybersecurity.
Nonconformance management: The process of reacting to a nonconformity, understanding the conditions that caused the nonconformity, and then taking steps to mitigate future nonconformities.
Nonconformance management software: Any software system designed to assist the process of reacting to a nonconformity, understanding the conditions that caused the nonconformity, and then taking steps to mitigate future nonconformities.
Nonconforming record (NCR): A database that contains every nonconforming condition that occurred during the existence of a company, manufacturing facility, or production run.
Nonconformity: A condition existing within a unit, process, or service that does not meet pre-existing criteria for acceptance.
Nondestructive testing and evaluation (NDT, NDE): A testing process that leaves a unit undamaged.
Nonvalue added: An operation that does not directly deliver value to the customer. Consider eliminating.
O
One-piece flow: A process whereby units move between stations in the production line as soon as each operation finishes.
Operating characteristic curve (OC curve): A data visualization that displays the probability that an individual lot (or group of lots) achieves acceptance.
Original equipment manufacturer (OEM): A business that accepts finished goods from several vendors and uses them to create a unique product.
Out of spec: A unit that fails to possess specific predefined characteristics.
Outputs: The units resulting from a manufacturing process.
Overall equipment effectiveness (OEE): The measurement of how well a machine performs in the real world versus how well it’s supposed to perform on paper.
P
Parallel operation: Speeding up production by having one operator work on each side of a machine.
Pareto chart: A root cause analysis tool designed to indicate a small number of causes producing the highest outcomes.
Percent chart: A control chart designed to evaluate process stability.
Physical transformation task: One of any process steps designed to transform raw materials into finished products.
Plan-do-check-act (PDCA) cycle: A quality improvement process involving making a plan, executing a plan, measuring the results of the plan, and then taking action to resolve any gap between predicted and actual outcomes.
Policy: A standing order allowing organizations to remain compliant with regulations.
Preventive action: A policy designed to stop nonconformances from occurring or recurring.
Problem concentration diagram: A heat map plotting accidents or nonconformances against physical locations within a plant or on a product itself.
Process analysis: A document used to improve process understanding to increase efficiency.
Process improvement: The act of increasing process efficiency, safety, or quality following a predefined objective.
Product audit: The process of inspecting a product to ensure that it conforms to the expectations of the product design team, regulatory bodies, and legal codes. Distinct from acceptance testing.
Production part approval process (PPAP): A type of audit originating with the automotive industry, designed to ensure that a new part from a new supplier can safely and seamlessly integrate into the existing production process without disrupting overall product quality.
Productivity: How much work can be produced within a stated timeframe.
Product or service liability: The amount of compensation required if a product or service damages property, injures a user or causes other harms.
Project management: The act of applying management techniques to a process to complete it on time and within budget.
Project planning tools: Tools and techniques used in project management.
Pull system: The process of replenishing inventory as needed instead of on schedule.
Q
Quality: The subject of this glossary.
Quality 4.0: Quality with added digital technologies.
Quality assurance/quality control (QA/QC): The process of either ensuring that the quality of a process or product matches a predefined standard or the process of managing quality until that standard is met.
Quality analytics: Insights into understanding an organization’s data pitfalls.
Quality analytics tools: Algorithms, charts, diagrams, and lookup tables used to identify anomalies and errors.
Quality audit: The process of inspecting a product or facility to ensure that a predefined quality standard has been met.
Quality costs: The cost of meeting and improving quality standards within a given process, plus any added cost when quality fails to meet an agreed-upon standard.
Quality engineering: The process of maximizing quality throughout the product lifecycle.
Quality function deployment (QFD): the process whereby manufacturers implement customer expectations during product development and manufacturing.
Quality loss function: A formula describing the monetary loss occurring when a manufacturing process fails to output products at the targeted quality level.
Quality management (QM): Managing a production process in a manner that achieves a targeted level of quality without deviances.
Quality management software: Software-based quality management tools. That may refer to a software-based quality management system (QMS) or any application fulfilling a quality function without rising to the level of a comprehensive QMS.
Quality management system (QMS): The sum of an organization’s formalized efforts to implement and improve quality.
Quality score chart: A chart that evaluates process stability by assigning a weight number to various events and creating a total quality score by adding the weighted numbers.
Queue time: The amount of time that a product or subassembly waits on the production line without being acted on.
Quick changeover: The process of modifying a machine quickly enough to run multiple products.
R
Random sampling: A technique where units are selected for inspection at random.
Recall: The process of ordering defective products to be returned to a facility for disposal or repair.
Rejection number: The number of defective products in a lot that, if reached, triggers the rejection of the lot as a whole.
Repeatability: The degree to which running a process the same way produces the same outcome.
Right sizing: The process of adapting manufacturing equipment and processes to the space inside the manufacturing facility.
Risk management: The process of understanding and mitigating potential accidents, defects, and other harms that may occur throughout the manufacturing process or product lifecycle.
Risk management software: Any software product that allows manufacturers or quality managers to record potential risks. In addition, any software that allows manufacturers or quality managers to record and implement strategies to prevent or mitigate these risks.
Root cause: The inciting factor behind an accident or nonconformance.
Root cause analysis: A quality management practice using techniques, like 5 Whys or Fishbone diagrams, to uncover the inciting factor behind an accident or nonconformance and then implement corrective action.
S
Sample: Any number of units pulled from a lot to be inspected for acceptance purposes.
SBAR: An acronym standing for Situation, Background, Assessment, and Recommendation, referring to a tool communicating critical information understandably during emergent situations.
Scorecard: A rubric that helps customers rate your services or products.
Service level agreement (SLA): An agreement between a customer and a provider whereby the provider guarantees a certain amount of performance, reliability, and support over a given time.
Single-piece flow: A manufacturing process in which products are moved between operational steps without any work-in-process between the steps.
Social responsibility: The idea that businesses are responsible for eliminating negative externalities that arise from their money-making ventures.
Standard in-process stock: The smallest number of parts necessary for workers to perform assembly and production processes.
Standard work: A system in which jobs within an assembly line are organized to create a sequence that creates no waste but is still defined by the limits of human motion.
Stop the line authority: Control given to workers or machines allowing them to halt production during abnormalities, allowing them to prevent defects or variations from passing.
Strengths, weaknesses, opportunities, threats (SWOT) analysis: A management-level technique used to steer an organization through periods of challenge.
Structural variation: Any predictable, long-term pattern of change within an organization’s output—a good example would be an increase in the production of notebooks before back-to-school shopping.
Supermarket: A storage repository for parts used during production.
Supplier quality: The overall quality of goods provided by a vendor.
Supplier quality assurance: The degree to which a supplier can guarantee the quality of the parts, components, or raw materials that it provides.
Supplier quality management: The process of working with a supplier to help them uphold the quality and conformance of the parts, components, or raw materials that it provides.
Supply chain: The totality of suppliers used to provide parts, materials, or raw materials to fuel a manufacturing process.
Supply chain quality:
T
Technical report (TR): A document you’ll be required to deliver as part of an ISO certification process.
Technical specification (TS): Another document you’ll be required to deliver as part of an ISO certification process.
Throughput: The measurement of how fast your completed inventory is sold and shipped to the customer.
Tolerance: The degree to which a product’s dimensions can vary before they represent a nonconformance.
Total quality: A method by which quality is imposed and continuously improved throughout the organization as part of a strategic imperative.
Total quality management (TQM): A top-down approach to quality, in which quality is imposed and continuously improved throughout the entire organization as part of a strategic imperative. This term can be used interchangeably with “Total Quality.”
Transaction data: Information generated during a process step, like the record produced when a worker replenishes a store of parts from inventory.
Tree diagram: A chart, often resembling a tree, delineating the primary and secondary steps necessary for completing a process or achieve an objective.
U
Unit: Most often refers to a single complete product but can also refer to a subassembly or a single raw material item.
Uptime: The measurement of time a service or piece of equipment is available for use measured against the time it is out of service.
V
Validation: The process of auditing or inspecting a product or service to ensure it is working as intended while conforming with laws and regulations.
Value added: Any process internal or external (i.e., marketing) to the manufacturing process helping improve customer satisfaction or salability.
Value analysis: The process of identifying value-added activities internal or external to the manufacturing process.
Value engineering: A design process that intends to minimize costs to the organization while maintaining customer requirements.
Value stream: The totality of processes (both value-added and not) required to create a product from raw materials and deliver it into the customer’s hands.
Value stream loops: The part of the value stream that extends between two supermarkets.
Value stream manager: The individual responsible for mapping and implementing the future state of the value stream.
Value stream mapping: the process of mapping the present and future state of the value stream.
Verification: The process of ensuring a process or product is compliant with legal or regulatory strictures.
Visual controls: Signage or dashboards that allow both workers and operators to check production status at a glance.
Voice of the customer: The collective desires and feedback of the customer base as related to your products or services and expressed using tools, including surveys, focus groups, social listening, and other information-gathering processes.
Voluntary standard: Any regulatory standard whose adoption is not mandatory based on law.
W
Waste: Any raw materials, components, or products that cannot be used or delivered to the customer. Any activities that consume time and resources that do not produce value for the organization.
Work in process: Items that have gone through a manufacturing operation and are now waiting for the next step.