Frontline workers are the backbone of the manufacturing industry. Increasingly, they are using devices such as mobile devices, wearables or apps to stay connected to the manufacturing process in real time and perform their roles more effectively. Workers who use these tools are known as “connected frontline workers.”
Integrating connected worker (CW) tools with an advanced quality management system (QMS) supports a holistic approach to quality (beyond simple compliance or quality control) and provides a seamless “shop floor to the top floor” solution.
The Role of Frontline Workers in Manufacturing Quality Management
Frontline workers play an essential role in upholding and executing quality management standards within the manufacturing industry. They face a set of unique challenges as part of their role.
Importance of Frontline Workers in Quality Assurance
Frontline workers are in an excellent position to identify product issues and suggest improvements, given their heavy involvement in production. They regularly conduct product inspections throughout the manufacturing process and report product deviations. Identifying and reporting issues as early as possible typically means fixing them, which will take less time and money and improve quality.
After identifying issues, frontline workers must communicate any quality assurance issues to quality control teams. Uncovering root causes enables corrective measures to be implemented. Meeting customer expectations builds trust and fosters loyalty.
Challenges Faced by Frontline Workers
Frontline workers are busy, and they typically have a lot of tasks to complete in a short space of time. Long hours are common, and the role is often demanding, which can result in stress and burnout. Consequently, issues can slip through the net, and there is a risk of them going unreported.
As well as leading to potential safety concerns, this can severely impact the quality of products. Workers must constantly monitor materials, machinery, and products to identify defects and ensure that everything meets the required standards.
The absence of advanced technological support in these processes makes the job even more challenging. Manual processes are tiring and increase the likelihood of oversights and mistakes.
ETQ Reliance Empowers Frontline Workers
ETQ Reliance® is a cloud-based platform that centralizes data and allows frontline workers to access it anywhere and at any time. Administrators can also set customizable access levels to assign different permissions to different groups of workers.
The platform’s interface is intuitive and easy to use and navigate, making it accessible to workers with a wide range of technical expertise.
Real-Time Data and Communication
ETQ’s QMS is a centralized system that allows everyone with permission to access the most up-to-date data whenever they need it. This leads to increased efficiency and makes collaboration easier. The platform also features tools enabling teams to discuss issues and collaborate in real time.
The software can also interface with enterprise resource planning (ERP), customer relationship management (CRM), and manufacturing execution system (MES) applications. This feature makes it easy for connected frontline workers to share data between different departments within the organization.
It also provides real-time dashboards and analytics, allowing workers, managers, and stakeholders to see an immediate overview of quality, performance, and trends.
Training and Compliance Management
Quality managers can use ETQ’s QMS as a centralized training repository that can be easily accessed anytime by those who need it. Managers can use the platform to schedule and manage training programs and set deadlines. They can also create customized learning paths based on workers’ roles.
After setting up the programs, managers can track workers’ progress and send automated notifications and reminders as required. Managers and workers receive timely alerts for near-expiring certifications and approaching compliance deadlines.
Enhanced Collaboration and Efficiency
ETQ Reliance helps streamline processes, reduce errors, and promote a culture of continuous improvement. These features foster enhanced collaboration between frontline workers and improve their efficiency.
Streamlining Processes and Reducing Errors
QMS software helps to streamline processes across the organization by providing the connected frontline worker with an established set of procedures. This strategy promotes consistency and reduces the number of errors caused by inconsistency. It also allows workflow automation, which reduces manual errors.
If errors occur, it’s possible to identify and solve them quickly thanks to the software’s real-time data capture, which gives managers a thorough overview of what is happening across the organization. This information helps to reduce risks and fosters a culture of continuous improvement.
Promoting a Culture of Continuous Improvement
QMS software fosters a culture of continuous improvement by promoting increased collaboration and communication. Doing so enhances organizational efficiency, enabling teams to complete tasks swiftly and adapt to changing needs.
It also gives the connected worker and manager thorough insight into their performance. This data makes it easier for managers to recognize employees and teams who contribute to process improvements and reward them accordingly.
Risk Management and Proactive Problem-Solving
ETQ’s QMS software bolsters risk management and proactive problem-solving capabilities among frontline workers. helps to foster a proactive approach to addressing potential issues so they can be dealt with before they escalate.
Identifying and Mitigating Risks
The connected frontline worker can identify and mitigate risks using ETQ’s QMS software. The software provides them with the tools to assess and analyze potential risks and monitor them closely.
If a connected frontline worker identifies a risk, they can use the platform to provide feedback. This data helps the organization improve its risk mitigation strategy and reduces the chance of this risk — or similar risks — becoming an issue in the future.
The connected worker can also use the QMS platform to deepen their understanding of potential risks and learn how to address them appropriately.
Proactive Problem-Solving and Preventive Measures
QMS software helps frontline workers proactively solve problems by providing access to real-time monitoring and reporting software. As a result, it’s possible to identify and address issues almost as soon as they happen. The connected frontline worker can also use the software to find the root cause of the issue and prevent it from happening again.
Use of a QMS allows managers to use the software to implement preventive measures to stop future issues from occurring. Its in-depth reporting provides workers with access to documentation and data regarding past issues to identify patterns or trends. They can take the appropriate action to stop these incidents from happening again.
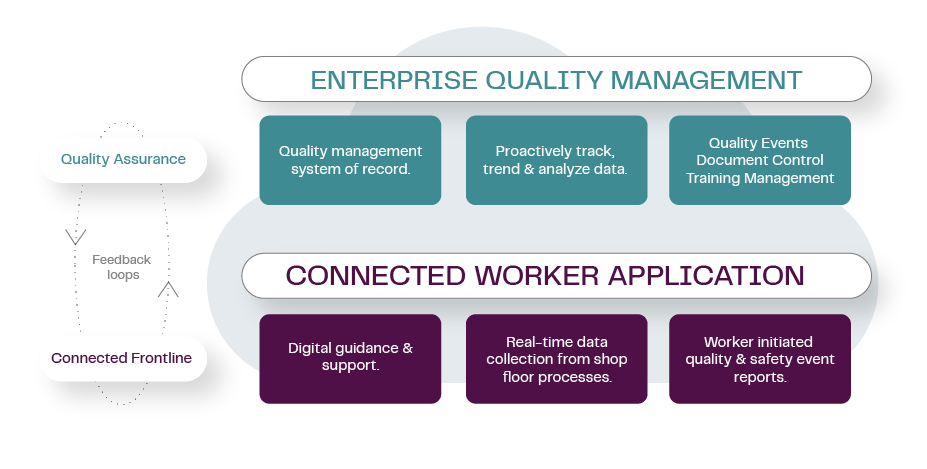
ETQ Reliance Connected Worker Solution
The ETQ Reliance Connected Worker has the tools to embed quality throughout your organization. From work instructions that help every worker build right the first time to issue handling that shuts down your hidden factory to reducing friction and process inefficiencies across the value chain.
Frontline manufacturing workers see opportunities daily to reduce risk and improve quality. However, managing critical quality processes with paper, spreadsheets or word of mouth is inefficient and impedes timely reporting and resolution of quality and safety issues. As a result, too many organizations miss obvious opportunities to improve product quality and reduce the costs associated with poor quality. To address the limitations of siloed, homegrown, and legacy systems, ETQ Reliance Connected Worker offers a unique digital solution that automates workflows between the frontline workforce and quality management teams.
Learn more about how ETQ Reliance empowers the connected worker and improves your quality management practices or request a demo today.